

Nossas publicações
Disseminar conhecimento e contribuir para o estado da arte são alguns dos nossos compromissos com a comunidade acadêmica.
Nesta página você pode conhecer alguns dos nossos artigos e coautorias, além de poder baixá-los gratuitamente.

Vibrational and Resistance Responses for Ether-Amine Solutions of the Buckypaper-Based Chemiresistor Sensor
Débora Ely Medeiros Ferreira, Paula Fabíola Pantoja Pinheiro, Luiza Marilac Pantoja Ferreira,
Leandro José Sena Santos, Rosa Elvira Correa Pabón and Marcos Allan Leite Reis
Nanomaterials, v. 15, 1197, 2025
https://doi.org/10.3390/nano15151197
Publicado: 05/08/2025
Abstract
The development of miniaturized sensors has become relevant for the detection of chemical/biological substances, since they use and detect low concentrations, such as flocculants based on amines for the mining industry. In this study, buckypaper (BP) films based on carboxylic acid functionalized multi-walled carbon nanotubes (f-MWCNTs) were produced through vacuum filtration on cellulose filter paper to carry out sensory function in samples containing ether-amine (volumes: 1%, 5%, 10% and 100%). The morphological characterization of the BPs by scanning electron microscopy showed f-MWCNT aggregates randomly distributed on the cellulose fibers. Vibrational analysis by Raman spectroscopy indicated bands and sub-bands referring to f-MWCNTs and vibrational modes corresponding to chemical bonds present in the ether-amine (EA). The electrical responses of the BP to the variation in analyte concentration showed that the sensor differentiates deionized water from ether-amine, as well as the various concentrations present in the different analytes, exhibiting response time of 3.62 ± 0.99 min for the analyte containing 5 vol.% EA and recovery time of 21.16 ± 2.35 min for the analyte containing 10 vol.% EA, revealing its potential as a real-time response chemiresistive sensor.
3D-printed metal-free thermal sensor based on PLA coated with PLA/CNTs nanocomposite ink
Leandro José Sena Santos, Luciano José Barbosa Quaresma, Dhonata Sebastião Caldas Oliveira, Pedro Paulo Rodrigues Pinheiro Filho, Kelly Costa Alves, Luiza de Marilac Pantoja Ferreira, Paula Fabíola Pantoja Pinheiro e Marcos Allan Leite dos Reis
Sensors and Actuators: A. Physical, v. 384, 116279, 2025
https://doi.org/10.1016/j.sna.2025.116279
Publicado online: 04/02/2025

Abstract
Metal-free devices such as the 3D-printed thermal sensors based on polymer/carbon nanotubes (CNTs), are presented as more sustainable solutions than conventional metal detectors. Biodegradability of poly(lactic acid) (PLA) has aroused interest in using it as a substrate and/or polymer matrix for CNT-based nanocomposites and, despite reports of improvements in mechanical properties, investigations on its thermoresistive and thermoelectric properties are still scarce. In this sense, aiming to evaluate the potential of PLA/CNTs as a thermoresistive and/or thermoelectric thermal sensor in the body temperature range, a commercial PLA filament was coated, via inverted immersion, with PLA/CNTs-based ink. This filament was used in the 3D printing of a flexible serpentine-shaped sensor, via fused filament fabrication, which was subsequently coated with PLA/CNTs ink. For comparison, a PLA-only sensor was also 3D-printed, and no coating was applied. The samples were analyzed via scanning electron microscopy (SEM), Raman spectroscopy and thermoresistive and thermoelectric tests. The incorporation of CNTs into the PLA matrix, proven by SEM and Raman modes, confers thermal sensitivity to the sensor, causing a periodic decrease/increase in electrical resistance upon heating/cooling with maximum response and response and recovery times around 4.61 %, 600 s and 560 s, respectively. Furthermore, the nanostructured sensor presented Seebeck effect, generating up to 400 μV from a temperature gradient of 12.6 K (thermoelectric power of 31.75 μV/K). Thus, these thermoresistive and thermoelectric effects show that the proposed nanostructured sensor can be a sustainable alternative to replace metal-based devices such as Pt100 thermistors and thermocouples.

Anisotropic piezoresistive response of 3D-printed pressure sensor based on ABS/MWCNT nanocomposite
Luciano J. B. Quaresma, Dhonata S. C. Oliveira, Rosielem S. Dias, Kelly C. Alves, Luiz G. D. de Barros, Gustavo Pessin, Amilton Sinatora, Waldeci Paraguassu & Marcos A. L. dos Reis
Scientifc Reports, v. 14, 25297, 2024
https://doi.org/10.1038/s41598-024-76028-2
Publicado: 25/10/2024
Abstract
Nanocomposites based on carbon nanotubes (CNTs) are suitable for sensors, due to matrix ability to incorporate nanotube properties. Thus, we developed a low-cost, nanostructured poly(acrylonitrile-butadiene-styrene) (ABS) polymer piezoresistive sensor produced by additive manufacturing. For this, solution layers of acetone, dimethylformamide and CNTs functionalized with carboxylic acid were pulverized on an ABS substrate using an aerograph. Electrical characterization revealed an anisotropic piezoresistive response of the material, induced by the printing lines direction. Field Emission Gun-Scanning Electron Microscopy showed the nanostructured film spreading after five layers of CNTs as well as the random entanglement of nanotubes on parallel and perpendicular 3D-printed ABS substrates. Raman spectroscopy indicated compression and p-type doping of CNTs in interaction with the polymer, as seen mainly by the blueshift of the G and 2D subbands. The results show that the material is promising for pressure sensors, with potential applications in robotic haptic feedback systems.
Effect of TiC-CNT precipitates on the microstructure and hardness of coatings welded by the GTAW process
Paula Fabíola Pantoja Pinheiro, Cristhian Ricardo Loayza Loayza, José Gedael Fagundes Júnior, Simone Patrícia Aranha da Paz, Eduardo de Magalhães Braga, Marcos Allan Leite dos Reis

Materials Letters, v. 377, 137490, 2024
https://doi.org/10.1016/j.matlet.2024.137490
Publicado: 01/10/2024
Abstract
Carbon nanotubes (CNT)-reinforced metal matrix nanocomposites balance toughness and ductility and, therefore, can reduce maintenance costs of industrial equipment. In this sense, flux-cored made of low carbon steel filled with CNT/Ti6Al4V/CaF2 were used as filler metal to coat an A131 grade A steel sheet via GTAW process. SEM and Raman spectroscopy analyses evidence the partial phase transformation between Ti and CNT in TiC-CNT precipitates, which can act as barriers to dislocation movements in a ferritic matrix. Consequently, the hardnesses of the coatings were up to 33.9–77.4 % higher than the base metal. Therefore incorporating TiC-CNT precipitate-based reinforcements via arc welding can improve the hardness of conventional steels.

Morphological and Doping Effects on Electrical Conductivity of Aluminum Metal Substrate through Pulsed Electrodeposition Coating of Cu-MWCNT
Alberto S. Silva, Mário E. S. Sousa, Eduardo M. Braga and Marcos A. L. Reis
Metals, v. 14, issue 9, 1060, 2024
https://doi.org/10.3390/met14091060
Publicado online: 17/09/2024
Abstract
The demand for more efficient and sustainable electrical systems has driven research in the quest for innovative materials that enhance the properties of electrical conductors. This study investigated the influence of copper (Cu) coating and multi-walled carbon nanotubes (MWCNTs) on aluminum metal substrate through the pulsed electrodeposition technique. Parameters such as the concentration of chemical elements, current, voltage, temperature, time, and electrode spacing were optimized in search of improving the nanocomposite coating. The metallic substrate underwent anodization as surface preparation for coating. Characterization techniques employed included Field Emission Gun—Scanning Electron Microscopy (FEG-SEM) for analyzing coating morphology, Energy-Dispersive X-Ray Spectroscopy (EDS), Raman spectroscopy, and Kelvin probe for obtaining surface electrical conductivity values. Homogeneous dispersion of the Cu-MWCNTs film coating was achieved across the entire surface of the aluminum plate, creating a complex morphology. The doping effect was highlighted by changes in the vibrational characteristics of the nanocomposite, which affected the Raman spectrum dispersion bands. An increase in surface electrical conductivity by ≈52.33% compared to the control sample was obtained. Therefore, these results indicate that the improvement in the material’s electrical properties is intrinsically related to the complex morphology achieved with the adopted Cu-MWCNT nanocomposite coating process.
Additive manufacturing of poly (lactic acid)/hydroxyapatite/carbon nanotubes biocomposites for fibroblast cell proliferation
Francilene da Luz Belo, Esleane Vilela Vasconcelos, Miriane Alexandrino Pinheiro, Damares da Cruz Barbosa Nascimento, Marcele Fonseca Passos, Alisson Clay Rios da Silva, Marcos Allan Leite dos Reis, Sérgio Neves Monteiro, Rebecca Thereza Silva Santa Brígida, Ana Paula Drummond Rodrigues & Verônica Scarpini Candido
Scientific Reports, v. 13, 20387, 2023
https://doi.org/10.1038/s41598-023-47413-0
Publicado: 21/11/2023
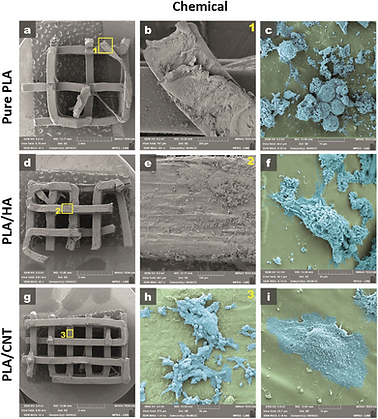
Abstract
Bone tissue is one of the most important in the human body. In this study, scaffolds of poly (lactic acid) PLA reinforced with hydroxyapatite (HA) and carbon nanotubes (CNT) were manufactured, evaluating their mechanical and biological properties. HA was synthesized by wet method and characterized by X-ray diffraction (XRD), Fourier transform infrared spectroscopy (FTIR), and scanning electron microscopy (SEM). The scaffolds were produced using additive manufacturing and characterized by optical microscopy, SEM, thermogravimetric analysis (TGA), Raman spectroscopy and biological tests. The SEM results showed that the PLA surface was affected by the incorporation of CNT. TG showed that the incorporation of HA into the polymer matrix compromised the thermal stability of PLA. On the other hand, the incorporation of CNT to the polymer and the impregnation with HA on the surface by thermal effect increased the stability of PLA/CNT scaffolds. Raman spectra indicated that HA impregnation on the surface did not modify the polymer or the ceramic. In the compression tests, PLA and PLA/CNT scaffolds displayed the best compressive strength. In the biological tests, more than 85% of the cells remained viable after 48 h of incubation with all tested scaffolds and groups with CNT in the composition disclosing the best results.

Periquiteira (Cochlospermum orinocense): A Promising Amazon Fiber for Application in Composite Materials
Miriane Alexandrino Pinheiro, Maurício Maia Ribeiro, Diemison Lira Santa Rosa, Damares da Cruz Barbosa Nascimento, Alisson Clay Rios da Silva, Marcos Allan Leite dos Reis, Sergio Neves Monteiro and Verônica Scarpini Candido
Polymers, v. 15, issue 9, 2120, 2023
https://doi.org/10.3390/polym15092120
Publicado online: 28/04/2023
Abstract
Natural lignocellulosic fibers (NLFs) have in recent decades appeared as sustainable reinforcement alternatives to replace synthetic fibers in polymer composite material applications. In this work, for the first time, the periquiteira (Cochlospermum orinocense), a lesser known NLF from the Amazon region, was analyzed for its density and, by X-ray diffraction (XRD), to calculate the crystallinity index as well as the microfibrillar angle (MFA), thermogravimetric analysis (TGA), Fourier transform infrared spectroscopy (FTIR), scanning electron analysis (SEM) and tensile strength. The apparent density found for the periquiteira fiber was 0.43 g/cm3, one of the NLF’s lowest. XRD analysis indicated a crystallinity index of 70.49% and MFA of 7.32°. The TGA disclosed thermal stability up to 250 °C. The FTIR analysis indicated the presence of functional groups characteristic of NLFs. The SEM morphological analysis revealed that the periquiteira fiber presents fine bundles of fibrils and a rough surface throughout its entire length. The average strength value of the periquiteira fiber was found as 178 MPa. These preliminary results indicate that the periquiteira fiber has the potential to be used as a reinforcing agent in polymeric matrices and can generate a lightweight composite with excellent mechanical properties that can be used in various industrial sectors.
Nanostructured 3D bioprinting of PLA with bioglass-CNT scaffolds for osseus tissue graft manufacturing
Esleane Vilela Vasconcelos, Francilene Belo da Luz, Simone Patrícia Aranha da Paz, Marcos Allan Leite dos Reis, Alisson Clay Rios da Silva, Marcele Fonseca Passos, Carlos Augusto Galvão Barboza, Sérgio Neves Monteiro, Verônica Scarpini Candido

Journal of Materials Research and Technology, v. 23, 5923-5938, 2023
https://doi.org/10.1016/j.jmrt.2023.02.171
Publicado online: 28/02/2023
Abstract
Bone involvement promoted by aging and accidents has raised interest in biomaterials and biofabrication technologies for bone regeneration purposes. Thus, 3D printing technology has gained prominence in the production of scaffolds due to its versatility in producing complex geometries with interconnected pores. In this work, composite scaffolds of poly (lactic acid) (PLA), bioglass (BG) and carbon nanotubes (CNT) were produced by 3D printing, using hexagonal, honeycomb-like geometry interspersed. The samples were analyzed in terms of chemical structure, crystallinity and morphology using Fourier transform infrared spectroscopy and Raman spectroscopy, X-ray diffraction and scanning electron microscopy, respectively. The thermal stability of the composite was evaluated by thermogravimetry and the mechanical properties by compression tests. The cell viability was determined by Alamar Blue. The results that raman spectroscopy confirmed the interaction of BG in the polymer matrix by new peaks in the spectrum between 1400 and 2600 cm−1 and the presence of the D, G and 2D bands of the CNTs. In terms of compressive strength, PLA scaffolds with 2 mm inner spacing demonstrated higher compressive strength of 14.88 ± 2.35 MPa, while PLA/CNT higher apparent compressive modulus of 0.58 ± 0.36 GPa. In cell viability, statistical tests showed that there was no significant difference between scaffolds with 2 and 4 mm inner spacing.
.jpg)
Buckypaper-Based Nanostructured Sensor for Port Wine Analysis
Luiza Ferreira, Paula Pinheiro, Newton Barbosa Neto and Marcos Reis
Sensors, v. 22, 9732, 2022
https://doi.org/10.3390/s22249732
Publicado: 12/12/2022
Abstract
The development of electronic gadgets has become of great relevance for the detection of fraud in beverages such as wine, due to the addition of adulterants that bring risks to human health as well as economic impacts. Thus, the present study aims to apply a buckypaper (BP) based on functionalized multiwalled carbon nanotubes (MWCNTs)/cellulose fibers as a sensor for the analysis of Port wine intentionally adulterated with 5 vol.% and 10 vol.% distilled water and ethyl alcohol. The morphology of BP characterized by scanning electron microscopy indicates the formation of agglomerates of random MWCNTs dispersed on the surface and between the fibers of the cellulosic paper. The analysis of the response of the film through the normalized relative resistance change showed a higher response of 0.75 0.16 for adulteration with 10 vol.% of water and a mean response time of 10.0 3.60 s and recovery of approximately 17.2 min for adulteration with 5 vol.% alcohol. Principal component analysis (PCA) was used in data processing to evaluate the ability of BP to recognize and discriminate analytes and adulterating agents, allowing the investigation of its potential application as a low-cost and easy-to-handle multisensor.
Stainless steel-CNT composite manufactured via electric arc welding
C.R. Loayza, D.C.S. Cardoso, D.J.A. Borges, A.A.F. Castro, A.C. Bozzi, M.A.L. Dos Reis, E.M. Braga
Materials & Design, v. 223, 111169, 2022
https://doi.org/10.1016/j.matdes.2022.111169
Publicado online: 17/09/2022
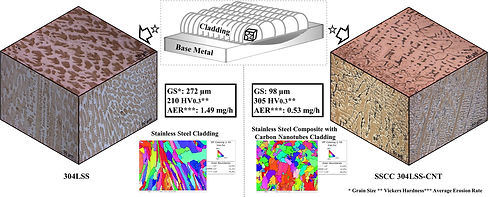
Abstract
Stainless-steel (SS) matrix composites reinforced by multi-walled carbon nanotubes (MWCNT) were successfully prepared by arc welding. A tubular rod was used as additional material. It was filled with a nanostructured flux-cored formed by 304L SS particles and MWCNT chemically treated with H2O2. The Raman spectra of the nanostructured flux-cored revealed an ID/IG rate drop from 1.12 to 0.68 and the amorphous carbon degree diminished from 76.5% to 17% after the chemical treatment. EBSD graphs demonstrated that the SS composite had a grain refinement of 64% induced by the nanotubes in the matrix, acting as nano-structured reinforcement. Compared with the 304L SS fabricated sample, the composite increased its microhardness by 45% (305 ± 15 HV0.3) and reduced its average erosion rate by 64% (0.53 ± 0.07 mg/h). The austenitic c(111) phase grows up after the vibratory cavitation test. Here, it was observed for the first time that the MWCNT influences the cavitation erosion strength in SS and that it is viable economically for large-scale industry.
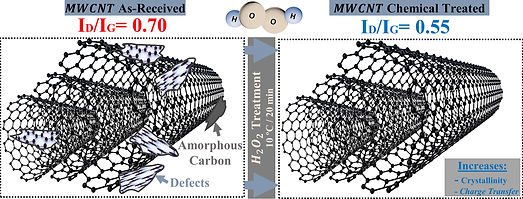
304L stainless steel particles bonded with MWCNT: Role of chemical treatment with H2O2
Cristhian R.L. Loayza, Eduardo M. Braga, Nielson F.P. Ribeiro, Diego J.A. Borges, Ivan G. Solorzano-Naranjo, Marcos A.L. Reis, Victor O. Ferreira
Diamond & Related Materials, v. 128, 109286, 2022
https://doi.org/10.1016/j.diamond.2022.109286
Publicado online: 02/08/2022
Abstract
This paper investigated the chemical treatment of MWCNT with AISI 304L stainless steel (304L SS) particles using hydrogen peroxide at both different temperatures (10 and 20 ◦C) and controlled reaction times (10 and 20 min). The sample treated at 10 ◦C for 20 min demonstrates an attenuation in the X-ray intensity of the metal particles of 42% and 55% at γ(111) and α(110) peaks, respectively. In addition, the deconvoluted Raman spectras reveal a crystallinity enhancement of up to 21% (ID/IG = 0.55) of the nanotube walls, reducing 76% of its amorphous carbon degree and displaying doping with a charge transfer of 0.0065 electrons (n doping) per carbon atom. SEM micrographs illustrate the particles' morphology and the dispersion of the nanomaterial. Futhermore, HR-TEM micrographs show the defects, impurities, and features on the inner and outer walls of the CNTs. In conclusion, both time and temperature variables affected the kinetic conditions for the chemical treatment of MWCNT using H2O2.
Thermoresistive and thermoelectric properties of coplanar cellulose-MWCNTs buckypaper
Paula Fabíola Pantoja Pinheiro, Luiza de Marilac Pantoja Ferreira, Fabrício Augusto dos Santos Rodrigues, José Carlos da Silva Oliveira, Anselmo Fortunato Ruiz Rodriguez, Mário Edson Santos de Sousa & Marcos Allan Leite dos Reis
Journal of Materials Science: Materials in Electronics, v. 33, pp. 17802–17813, 2022
https://doi.org/10.1007/s10854-022-08645-4
Publicado online: 24/07/2022

Abstract
Thermoresistive sensors are based on the change in electrical resistance with temperature variation, are easily read, and have a simple design but require external power for their operation. Thermoelectric devices (TDs) based on the Seebeck effect directly convert heat into electrical power without any moving parts, generating voltages from the temperature difference established between the ends of a solid-state material. In recent years, several thermoresistors and TDs have been manufactured with conductive films based on carbon nanotubes (CNTs), i.e., with buckypaper (BP), because they provide lightweight, flexible, and sensitive devices. Nevertheless, the electrical resistance and thermoelectric properties of CNTs are affected when they are randomly assembled to form a BP. Then, this study investigated the thermoresistive and thermoelectric properties of a coplanar BP with an active area of 1.0 cm2. Morphological characterization was performed by scanning electron microscopy and showed bundles of multiwalled CNTs agglomerated on the surface but also impregnated into cellulose fibers. BP-based thermoresistive sensor had a maximum sensitivity of -10.05% at 322 K. Moreover, the thermoelectric configuration presented a maximum thermovoltage and thermoelectric power of -1.2 mV and -0.09 mV/K, respectively. These results suggest that this coplanar BP can be easily applied in thermal sensors and thermoelectric device concepts.

SIMULTANEOUS IMPROVEMENT OF THE ELECTRIC CONDUCTIVE AND MECHANICAL PROPERTIES OF NANOSTRUCTURED ALUMINUM ALLOY
Prazeres E. R., Loayza C. R. L., Reis V.S., Melo V. L.; Quaresma J. M. V.; Dos Reis M. A. L.; Silva J. A.S. and Braga E. M.
International Journal of Development Research, v. 11, issue 06, pp. 56448-56452, 2022
http://www.journalijdr.com/simultaneous-improvement-electric-conductive-and-mechanical-properties-nanostructured-aluminum-alloy
Publicado online: 22/06/2022
Abstract
Aluminum nanocomposites demonstrate improvements in mechanical properties, as well as in thermal and electric conductivity. The incorporation of multiwalled carbon nanotubes (MWCNT) in the aluminum matrix, using conventional melting methods, is a long-standing issue. In this paper, Aluminum nanocomposites were fabricated via conventional casting method, using a nanostructured stainless-steel (SS) powder. Carbon nanotubes were treatedwith hydrogen peroxide, which led toan attachment tothe metal matrix particles. In this sense, the SS powder, added as an element alloy, refinedthe grains, and the CNT led the electric conductive to a better performance. Given this, the best alloy analyzed presented an approximate 10% increase in all of its characterized properties, therefore presenting a microhardness of 48 HV, aUltimate Tensile Stress of 183 MPa, and an electrical conductivity of 67% of IACS.
Electrical Properties of Iodine-Doped Cu/f-CNT Coated Aluminum Wires by Electrophoresis with Copper Sulfate Solution
Fabrício Rodrigues, Paula Pinheiro, Mário Sousa, Rômulo Angélica, Simone Paz and Marcos Reis

Metals, v. 12, 787, 2022
https://doi.org/10.3390/met12050787
Publicado: 03/05/2022
Abstract
This work investigated the effects of iodine on copper/functionalized carbon nanotubes (Cu/f-CNT) that were used in the coating of 1350 Aluminum Alloy wires, using the process of electrophoretic exposure with a solution of copper sulfate and iodine, under an electrical current of 1.2 A and a voltage of 10 V. The Al@Cu/f-CNT was characterized by Scanning ElectronMicroscopy in Secondary Electron mode, X-ray Diffraction and Raman spectroscopy, in addition to electrical measurements, at room temperature and under heating, via kelvin bridge. The results showed an increase of approximately 18% in the electrical conductivity of the IACS compared to the standard aluminum conductor, due to the iodine doping of the outer walls of the f-CNT, causing an expansion between the layers, and reflecting the increase in the conduction channels. This method of electrodeposition of Cu/f-CNT on the surface of metallic wires shows promise for the production of nanostructured cables with high ampacity, lightness and high performance, for application in power transmission lines.

Effects of CNTs addition on the microstructure and microhardness of stainless steel alloy/carbon-manganese non-alloyed steel welding
Marcos AL dos Reis, Mário ES de Sousa, André A Ferreira, Íris SM Carneiro, Clarissa H de Melo, Marcionilo NS Junior and Manuel F Vieira
Journal of Composite Materials, v. 55, issue 22, pp. 1-9, 2021
https://doi.org/10.1177/00219983211007201
Publicado online: 04/04/2021
Abstract
In recent years some progress has been made about the addition of Carbon Nanotubes (CNTs) in the stainless steel metal matrix by pulsed Gas Tungsten Arc Welding (P-GTAW). Despite that, there is lack of information regarding to microstructural modifications induced by CNTs in dissimilar welding. In this sense, we present the welding of nanocomposite based on Nickel/Carbon Nanotubes stainless steel 316L alloy (Ni/CNTs-SS 316L), as the welding metal, on carbon-manganese (C-Mn) non-alloyed structural steel, as the base metal. The microstructure of manufactured specimens with/without nanocomposite was characterized by: optical microscopy; Raman spectroscopy; scanning electron microscopy with energy dispersive spectroscopy (SEM-EDS) and electron backscattering diffraction (EBSD). Moreover, Vickers tests were performed from the welding metal (WM) to the base metal (BM) before/after temper treatment in order to investigate the microhardness changes. The results show that dilution rate and grain size for specimen with nanocomposite was higher than without nanocomposite; the CNTs affected the misorientation angle and texture of the WM; the topside microhardness from WM with Ni-CNTs was on average 30.40% higher than BM; and, in transverse cross-section microhardness was 31% higher than control sample on average at fusion line zone. These results indicate that addition of CNTs in the metallic matrix by dissimilar welding is a fertile ground for new studies applicable to manufacturing industry.
Cast Aluminum Surface Reinforced with Carbon Nanotube via Solubilization Treatment
Paulo R. O. Brito, Cristhian R. L. Loayza, Mário E. S. Sousa, Eduardo M. Braga, Rômulo S. Angélica, Simone P. A. da Paz and Marcos A. L. Reis
Metals and Materials International, v. 28, pp. 802-810 , 2021
https://doi.org/10.1007/s12540-020-00914-3
Publicado: 19/01/2021

Abstract
Carbon nanotubes (CNTs) are noteworthy, as they reinforce the metallic matrix, due to mechanical properties, such as the ~ 1.0 TPa Young module. To improve the maintenance of the commercially pure aluminum surface, multi-walled carbon nanotubes were incorporated into the aluminum surface with heat treatment by solid solubilization, in order to improve the surface properties of aluminum. The aluminum samples were chemically attacked for 30, 60 and 120 s and placed in a container with CNTs, being subjected to a temperature of 640 °C for 1 h. Then, the roughness was evaluated by a roughness meter for morphology in the scanning electron microscopy. An intensity of aggregation of CNTs was evaluated by XRD, and the Raman Spectra has evaluated the transfer of charge to the matrix. Microhardness was performed to evaluate the influence of the incorporation of CNTs in the matrix. The results obtained show that the incorporation of CNTs in the aluminum matrix increases the hardness in approximately 20% of the surface, in comparison with the control sample. The process of incorporating CNTs into the aluminum matrix by solubilization is a promising, simple and inexpensive alternative to improve the durability of the aluminum surface.
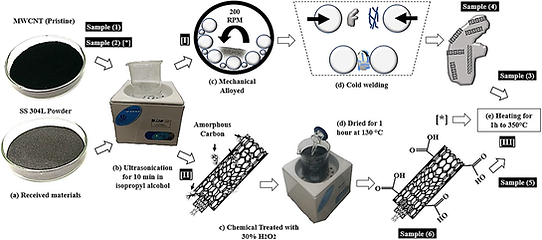
Stainless steel weld metal enhanced with carbon nanotubes
D. J. A. Borges, D. C. S. Cardoso, E. M. Braga, A. A. F. Castro, M. A. L. Dos Reis & C. R. L. Loayza
Scientific Reports, v. 10, 1777, 2020
https://doi.org/10.1038/s41598-020-75136-z
Publicado: 21/10/2020
Abstract
This paper aims to establish the most indicated route to manufacture a nanostructured powder composed of 5 wt% Multi-walled Carbon Nanotubes and 304LSS powder. Four specimens were prepared using Mechanical Alloying and Chemical Treatment (CT) with Hydrogen Peroxide (H2O2) as the main processes. A thermal treatment post-processing was used in half of the samples to remove the remaining amorphous carbon and to evaluate its effects. Regarding the powder analysis, attachment, amorphous carbon degree, crystallinity, and doping of the CNT throughout the metal matrix were investigated. The nanostructured powders were then inserted as a core in a 304LSS tubular rod to perform the arc welding process. The CT route eliminated the amorphous carbon and generated more refiner grains, which provided a cross-section hardness gain of more than 40% regarding the 304LSS joint. In summary, the CT route, combined with the GTAW process, provided a new method for nanocomposite manufacturing by combining shorter preparation steps, obtaining an improvement in the microstructural and hardness performance.
X-Ray Diffraction Analysis of Residual Stresses in the Premium Rails Welded by Flash Butt Process
Bras Senra de Oliveira, Lino Alberto Soares Rodrigues, Ednelson Silva Costa, Eduardo de Magalhaes Braga, Marcos Allan Leite dos Reis
Soldagem & Inspeção, v. 25, e2529, 2020
https://doi.org/10.1590/0104-9224/SI25.29
Aceito: 29/06/2020
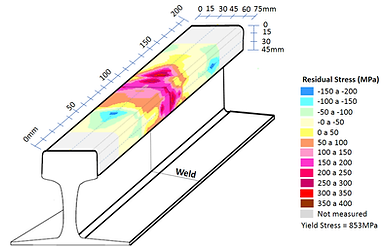
Abstract
This work is distinguished by searching for a non-destructive technology, and X-ray diffraction was validated by the XStress 3000 analyser. Measurements of residual stresses in the welded zone of premium pearlitic rails was performed, rail surface hardness of 370 HB and 0.79% carbon content. The welding of the rails was done by flash butt process, performed by Schlatter GAAS 80 stationary equipment. The results of the tensile and compressive stress measurements identified the residual stresses in the welded zone, with specific zones of tensile stresses misplaced at the weld center, with values up to 391 MPa, and compressive stresses, with values up to -166 MPa, as it moves away rails weld center. An important point of this study is the residual stress measurement considering a complete welding process, including: pre-grinding, flash butt welding, heat treatment, finishing grinding and straightening. Lastly, was observed the welding technique potentially can induce residual stresses at rails.

Doping charge transfer in Pt/CNT systems induced by laser power heating
A.C. Oliveira, M.A.L. Reis, F.F. de Sousa, M.E.S. Sousa
Chemical Physics, v. 530, 110591, 2020
https://doi.org/10.1016/j.chemphys.2019.110591
Publicado online: 11/11/2019
Abstract
Pt nanoparticles were dispersed on bamboo-like multiwall carbon nanotubes (Pt/CNTs). Raman Scattering effects were evaluated using distinct excitation laser powers e.g., from 1.0 to 6.0 mW over the Pt/CNTs. The charge transfer for the doping mechanism was investigated by Raman scattering and theoretical calculations. The sample was characterized via transmission electron microscopy and resonant Raman spectroscopy. The positions and widths of Raman G, G′-bands were analyzed based in the deconvolution of the bands. The laser power was varied from 1 to 4 mW closely related to the local temperature of 460, 540 and 500 K, respectively. This corresponded to the computed to Ginner and Gouter components displacements to low frequencies of ca. 20 and 15 cm−1. The results suggested a dependence of the laser power heating effect on the properties of the Pt/CNTs. Considerations about the destruction of walls surrounding particles are taken into account based on these results. Also, electron transfer to the MWCNTs with increase of the variation laser power was observed. Theoretical approaches for the intercalation stages of Pt on MWCNT were performed to verify the density of electronic states. The results indicated that the system exhibited a metallic behavior without Pt nanoparticle and stage 1 (stg #1), which show indeed energies gap is due to presence of Pt, and other stages is according with the experimental data.
Thermoelectric Effect of Buckypaper/Copper Assembly
Paula Fabíola Pantoja Pinheiro, Luiza de Marilac Pantoja Ferreira, Fabrício Augusto dos Santos Rodrigues, José Carlos da Silva Oliveira, Anselmo Fortunato Ruiz Rodriguez, Mário Edson Santos de Sousa and Marcos Allan Leite dos Reis
Journal of Nanotechnology, v. 2019, Article ID 8385091
https://doi.org/10.1155/2019/8385091
Publicado: 13/10/2019

Abstract
Carbon nanotubes (CNTs) exhibit excellent electrical and thermal properties that have been used in several device assemblies, such as electrode sheets made from an aggregate of CNTs, also called as buckypaper (BP). Despite that, the properties of single CNTs are reduced when randomly assembled to form a BP. In this way, this study investigated the thermoelectric effect of a BP electrode assembled on a copper electrode with an active area of 4.0 cm2. +e micrographs were obtained by scanning electron microscopy and show morphology agglomerated of multiwalled CNTs, which permeated into the filter paper, forming a thickness of 67.33 µm. Moreover, indoor/outdoor tests were performed approaching the BP electrode from a heat source. Thus, the electrical responses in function of temperature variation show maximum thermovoltages of 9.0mV and 40.73 mV from indoor and outdoor tests, respectively. Finally, an average Seebeck coefficient for the BP/copper electrodes array of 35.34 ± 6.0 mV/K was estimated from 298 to 304 K. These findings suggest that this assembly will be easily applied in thermoelectric device concepts.

Adsorption of chromium (VI) on hydrotalcite hydroxyapatite material doped with carbon nanotubes: Equilibrium, kinetic and thermodynamic
study
E. Rodrigues, O. Almeida, H. Brasil, D. Moraes, M.A.L. dos Reis
Applied Clay Science, v. 172, pp. 57-64, 2019
https://doi.org/10.1016/j.clay.2019.02.018
Aceito: 19/02/2019
Abstract
Hexavalent chromium adsorption in aqueous solution was studied in a fixed bed column with a hydrotalcitehydroxyapatite (HT-HAp) material doped with carbon nanotubes (CNT) at 333.15 K. Equilibrium, kinetic and thermodynamic behaviors were the focus of this work. The CNT doping was performed in two different proportions (5 and 15%wt.). Isotherm (Langmuir, Freundlich, Temkin, Redlich Peterson, Sips, and Toth) and kinetics (Thomas, Yoon-Nelson, and Adams–Bohart) models were tested. HT-HAp/CNT15 sample presented the best Cr(VI) bated proportion (76.97%R). The adsorption behavior was fit by the Freundlich model, following a pseudo second order kinetic mechanism confirmed by Thomas model. Thermodynamic parameters indicated a physisorption process.
Microstructural Characterization of Carbon Nanotubes (CNTs)-Reinforced Nickel Matrix Nanocomposites
Sónia Simões, Íris Carneiro, Filomena Viana, Marcos A. L. Reis and Manuel F. Vieira
Microscopy and Microanalysis, v. 25, Issue 1, pp. 180-186, 2019
https://doi.org/10.1017/S1431927618015064
Publicado: 01/02/2019

Abstract
This research focuses on the microstructural characterization of nickel matrix composites reinforced by carbon nanotubes (CNTs). The nanocomposites were produced by a conventional powder metallurgy process and the dispersion of CNTs and mixture with nickel powders was performed in a single step by ultrasonication. Microstructural characterization of Ni–CNT nanocomposites was performed by scanning and transmission electron microscopy, electron backscattered diffraction, high-resolution transmission electron microscopy, selected area electron diffraction, and fast Fourier transform analyses. This characterization revealed CNTs embedded in the nickel grains and mainly presented as clusters at the grain boundaries. CNTs hinder recrystallization during sintering, and dislocation cells and subgrains form as a result of the recovery process.

A new approach for the reinforcement of SS 304L via arc welding: Using nanostructured flux cored electrode
Cristhian R. Loayza L., Diego J.A. Borges, Danyella C.S. Cardoso, Paulo D.C. Assunção, Victor O. Ferreira, Paola E.C. Baia, Ademir A. Castro F., Marcos A.L. Reis, Eduardo M. Braga
Diamond & Related Materials, v. 92, pp. 138-145, 2019
https://doi.org/10.1016/j.diamond.2018.12.006
Publicado online: 15/12/2018
Abstract
Carbon nanotubes (CNT) are revolutionary materials and, since its discovery, the scientific community seeks ways to use the unique electrical and mechanical properties of CNT as in nanocomposites, incorporated in metal matrices via processes such as welding and thermal spraying. Despite an increasing number of researches involving the success in incorporating CNTs in metals, such as copper and aluminum, the knowledge concerning the use of stainless steel (SS) as metal matrix is yet underdeveloped. This paper uses the Mechanical Alloying (MA) process to incorporate Multi Walled Carbon Nanotubes in a Stainless Steel (SS) 304L powder. The mixture of SS 304L and 5 wt% MWCNTs was placed in a planetary ball mill along with a ball-to-powder ratio of 30:1, and rotated at 200 rpm. Samples with 0 min, 30 min, 60 min and 90 min of MA process were collected to be characterized using X-ray Diffraction (XRD), Raman spectroscopy and Scanning Electron Microscope (SEM). The results indicated that the 60 min sample achieved homogeneous dispersion and aggregation in the metal matrix, which qualifies such parameters as more suitable to produce the nanostructured powder of 304LSS-CNT. Thus, for the nanostructured cored flux electrode conception, a tubular electrode was filled with 304LSS-CNT powder from 0 min and 60 min of MA for welding via Pulsed Gas Tungsten Arc Welding (P-GTAW). Vickers hardness tests analyzed the mechanical properties, with 25% and 30% improvement of lateral hardness for the 60 min of MA, if compared to 0 min and SS powder only, respectively.
Composite Based on Biphasic Calcium Phosphate (HA/β-TCP) and Nanocellulose from the Açaí Tegument
Rachel M. B. Valentim, Sabina M. C. Andrade, Maria E. M. dos Santos, Aline C. Santos, Victor S. Pereira, Izael P. dos Santos, Carmen G. B. T. Dias and Marcos A. L. dos Reis
Materials, v. 11, issue 11, 2213, 2018
https://doi.org/10.3390/ma11112213
Publicado: 08/11/2018
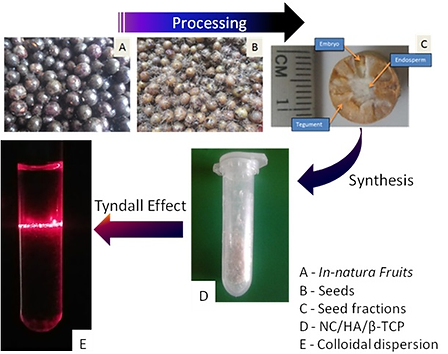
Abstract
The use of lignocellulosic remnants of the açaí agro-business will benefit the environment with a precursor material for biomedical applications. Nanocellulose (NC) allows the biomimetic growth of biphasic ceramics on its surface, with characteristics compatible with bone tissue, including bioactive properties and biocompatibility. In this study, the composites were obtained from açaí tegument (Euterpe Oleracea Mart.) NC using acid hydrolysis. The characterization performed by scanning electron microscopy showed the characteristic crystals of hydroxyapatite (HA) and calcium triphosphate (β-TCP) based on the results of X-ray diffraction, with the peak at 22°, showing the NC nucleation of HA and peak at 17° showing tricalcium phosphate (β-TCP). Fourier transform infrared spectroscopy confirmed the presence of O-H at 3400 cm-1 and C-H at 2900 cm-1, which is characteristic of cellulose; peaks were also observed at 1609 cm-1, verifying the reduction in lignin content. Groups (PO4)-3 at approximately 1070 cm-1, P-OH at 910–1040 cm-1, and (HCO3)-1 at 2450 cm-1 confirmed the formation of HA and β-TCP. The zeta potential had a range of -11 ± 23.8 mV related to particle size, which had a range of 164.2 × 10-9 – 4748 × 10-9 m.

Electrostatic Shielding of Faraday’s Ring Made of Stainless Steel 304 in the Glass Insulators
José Eduardo R. da Silva, Paula Fabíola P. Pinheiro and Marcos Allan L. dos Reis
Material Science and Engineering with Advanced Research, v. 2, issue 3, pp. 15-18, 2018.
https://doi.org/10.24218/msear.2018.28
Publicado: 30/05/2018
Abstract
High voltage glass insulators are equipment used in power transmission or distribution networks. They consist of a metal bell, a metal pin and a glass or porcelain disk. The joint action of atmospheric pollution, humidity and an intense electric field on the surface of these insulators accelerates the process of corrosion in the metal pin parts, resulting in catastrophic failures in the entire electrical system. In this sense, this case report presents an electrostatic protection device that, aiming to shield the surface of the pins against the pernicious electrical influences, was designed as a screwable Faraday cage made of stainless steel 304 and was denominated “Faraday’s ring”. To validate the efficacy of the device, electrical field simulations were carried out in 2D models of chains of insulators, which were developed using software that is based on the Finite Element Method, and experimental tests were also carried out with the aid of a Tesla Coil to supply electric discharges on the metallic surface of the device. The simulations and experimental results showed that the device was able to cancel out the intense electric field of ~3 x 103 kV/m in the outer surface and avoid the onset of corrosion within.
Síntese e caracterização do material hidrotalcita hidroxiapatita dopado com nanotubos de carbono e sua aplicação na catálise da reação de transesterificação
E. Rodrigues, H. Brasil, T. Barros, C. Pereira, M. A. L. dos Reis, O. Almeida
Cerâmica, v. 64, pp. 166-175, 2018
http://dx.doi.org/10.1590/0366-69132018643702230
Publicado: abr-jun/2018

Abstract
Este trabalho teve por objetivo a síntese e caracterização do material hidrotalcita-hidroxiapatita (HTHAp) dopado com três diferentes proporções (1, 5 e 15% p/p) de nanotubos de carbono (NTC) a fim de avaliar seu potencial como catalisador heterogêneo na reação de metanólise do óleo de soja. A síntese do material HTHAp foi realizada pelo método de coprecipitação (10≤pH≤11) com homogeneização ultrassônica e tratamento hidrotérmico a 80 °C. DRX, MEV/EDS, FT-IR, Raman, fisissorção de N2 e TG/ DTA foram as técnicas de caracterização utilizadas. A amostra HTHAp1NTC, dopada a 1% p/p, foi testada como catalisador em duas condições de temperatura (180 e 240 °C), 4 h de tempo de reação, carga de 2,5% de catalisador e razão álcool:óleo de 12:1. A dopagem contribuiu para melhorar propriedades estruturais, morfológicas e a estabilidade térmica do material. Os resultados de rendimento obtidos de 35,2% (180 °C) e 40,5% (240 °C) qualificam o material HTHAp dopado com NTC como catalisador em potencial na reação de transesterificação.

Raman spectroscopy fingerprint of stainless steel-MWCNTs nanocomposite processed by ball-milling
Marcos Allan Leite dos Reis, Newton Martins Barbosa Neto, Mário Edson Santos de Sousa, Paulo T. Araujo, Sónia Simões, Manuel F. Vieira, Filomena Viana, Cristhian R. L. Loayza, Diego J. A. Borges, Danyella C. S. Cardoso, Paulo D. C. Assunção and Eduardo M. Braga
AIP Advances, v. 8, 015323, 2018.
https://doi.org/10.1063/1.5018745
Publicado online: 24/01/2018
Abstract
Stainless steel 304L alloy powder and multiwalled carbon nanotubes were mixed by ball-milling under ambient atmosphere and in a broad range of milling times, which spans from 0 to 120 min. Here, we provided spectroscopic signatures for several distinct composites produced, to showthat the Raman spectra present interesting splittings of the D-band feature into two main sub-bands, D-left and D-right, together with several other secondary features. The G-band feature also presents multiple splittings that are related to the outer and inner diameter distributions intrinsic to the multiwalled carbon nanotube samples. A discussion about the second order 2D-band (also known as G'-band) is also provided. The results reveal that the multiple spectral features observed in the D-band are related to an increased chemical functionalization. A lower content of amorphous carbon at 60 and 90 min of milling time is verified and the G-band frequencies associated to the tubes in the outer diameters distribution is upshifted, which suggests that doping induced by strain is taking place in the milled samples. The results indicate that Raman spectroscopy can be a powerful tool for a fast and non-destructive characterization of carbon nanocomposites used in powder metallurgy manufacturing processes.
Incorporation of AWS 316L wire nanostructured with nickel-carbon nanotube by arc welding
Cristhian RL Loayza, Paulo DC Assunção, Danyella CS Cardoso, Diego JA Borges, Ademir AC Filho, Marcos AL Reis and Eduardo M Braga
Journal of Composite Materials, v. 52, issue 4, pp. 1899-1906, 2017
https://doi.org/10.1177/0021998317735880
Publicado online: 17/10/2018

Abstract
Carbon nanotubes have certain properties, such as 150 GPa tensile strength, a 1000 GPa shear modulus, an electrical conductivity of 60 S/m, and a high thermal conductivity of 2500 W/mk, that make them an optimum metallic matrix composite reinforcement. Otherwise, arc welding is a common industrial process that joins almost all metals. However, there are hardly any studies involving the addition of carbon nanotubes in stainless steel so far. In this research, we show the incorporation of an AWS 316L nanostructured wire with nickel-carbon nanotubes in austenitic stainless steel via pulsed gas tungsten arc welding, which formed nanocomposites with 0.75 and 1.5 wt% carbon nanotube contents in the wire. The characterization was performed by scanning electronic microscope, Raman spectroscopy, and X-ray diffraction. The Vickers microhardness test was used to analyze the mechanical properties. The nanostructure composite had microstructure modification, and superficial microhardness improved in 35% for 0.75 wt% carbon nanotube.

Multiwall carbon nanotubes filled with Al4C3: Spectroscopic signatures for electron-phonon coupling due to doping process
P.T. Araujo, N.M. Barbosa Neto, M.E.S. Sousa, R.S. Angélica, S. Simões, M.F.G. Vieira, M.S. Dresselhaus, M.A. Leite dos Reis
Carbon, v. 12, pp. 348-356, 2017.
http://dx.doi.org/10.1016/j.carbon.2017.08.041
Publicado online: 23/08/2017
Abstract
The spectroscopic signatures related to doping mechanisms in multiwall carbon nanotubes filled with aluminum carbide (Al4C3@MWCNTs) were studied and interpreted relative to changes in their electronic and phononic structures. UnfilledMWCNTs were used as standard samples to help interpreting the filling and the doping processes. The samples were characterized via scanning electron microscopy, transmission electron microscopy, X-ray diffraction and resonant Raman spectroscopy. The electron phonon coupling mechanisms associated to the Raman intensities, frequencies and linewidths of the G- and G'-band Raman modes were analyzed and connected to the doping mechanism in these multi-walled systems. Our results indicate that the Al4C3 particles transfer electrons to the MWCNTs. In order to shed light into the experimental findings, theoretical calculations were performed using two examples of filled and unfilled achiral MWCNTs and the results for the density of electronic states indicate that the two systems under consideration, exhibit metallic behavior, with aluminum carbide doping the carbon nanotubes, thereby supporting our experimental observations.
Effect of functionalization and size of CNTs in the production of nanocomposites
Sónia Simões, Paulo J. Ferreira, Filomena Viana, Marcos A.L. Reis and Manuel F. Vieira
Microscopy and Microanalysis, v. 23, S1, pp. 1942-1943, 2017
https://doi.org/10.1017/S1431927617010376
Publicado online: 04/08/2017

Abstract
Metal matrix composites (MMCs) generally offer a wide range of properties, such as high specific strength stiffness and good wear resistance. Carbon-based nanomaterials, in particular carbon nanotubes (CNTs), graphene or nanodiamonds, became very attractive as reinforcements for MMCs. Specifically, CNTs have received great attention from the research community due to their extraordinary properties, such as high stiffness, high strength and high thermal conductivity, combined with their low weight [1]. However, the dispersion of these nanofillers remains to be a major challenge during the production of the nanocomposites [2,3]. In this context, functionalization of CNTs may promote a better dispersion, but the mechanical properties of the composites may be impaired by damage of CNTs during the process. Several studies have been carried out to develop new techniques to obtain a good and uniform dispersion of CNTs throughout the matrix. Nevertheless, there are few studies analyzing the effect of length, outer diameter and surface modification of CNTs on the production of MMCs. In this context, the focus of this work is the study of the effect of size and functionalization of CNTs in the production of Al/CNTs nanocomposites. Prior to this work, ultrasonication was used to simultaneously disperse the CNTs and mixture them with Al powders. This approach proved to be a good option to produce Al/CNTs nanocomposites with a significant increase in mechanical properties [3]. However, the use of different CNTs, especially those that are functionalized, can improve the dispersion and promote the production of nanocomposites with better mechanical properties.

Aluminum and Nickel Matrix Composites Reinforced by CNTs: Dispersion/Mixture by Ultrasonication
Sónia Simões, Filomena Viana, Marcos A. L. Reis and Manuel F. Vieira
Metals, v. 7, issue 7, 279, 2017.
https://doi.org/10.3390/met7070279
Publicado: 22/07/2017
Abstract
The main challenge in the production of metal matrix composites reinforced by carbon nanotubes (CNTs) is the development of a manufacturing process ensuring the dispersion of nanoparticles without damaging them, and the formation of a strong bond with the metallic matrix to achieve an effective load transfer, so that the maximum reinforcement effect of CNTs will be accomplished. This research focuses on the production by powder metallurgy of aluminum and nickel matrix composites reinforced by CNTs, using ultrasonication as the dispersion and mixture process. Microstructural characterization of nanocomposites was performed by optical microscopy (OM), scanning and transmission electron microscopy (SEM and TEM), electron backscattered diffraction (EBSD) and high-resolution transmission electron microscopy (HRTEM). Microstructural characterization revealed that the use of ultrasonication as the dispersion and mixture process in the production of Al/CNT and Ni/CNT nanocomposites promoted the dispersion and embedding of individual CNT in the metallic matrices. CNT clusters at grain boundary junctions were also observed. The strengthening effect of the CNTs is shown by the increase in hardness for all nanocomposites. The highest hardness values were observed for Al/CNT and Ni/CNT nanocomposites, with a 1.00 vol % CNTs.
Electrical and Tensile Properties of Carbon
Nanotubes-Reinforced Aluminum Alloy 6101 Wire
Fabrício Augusto dos Santos Rodrigues, Waldeci Paraguassu, Sónia Simões, Manuel F. G. Vieira, José Antônio da Silva Souza, Eduardo de Magalhães Braga, and Marcos Allan Leite dos Reis
Journal of Nanoscience and Nanotechnology, v. 17, n. 7, pp. 4837-4841, 2017
https://doi.org/10.1166/jnn.2017.13429
Publicado: jul/2017

Abstract
The wires from aluminum alloy 6101 (AA-6101) used in power cables were covered by carbon nanotubes (CNTs) and graphite powders, and then they were subjected to solubilization heat treatment at a temperature of 550 C and aged at 180 C. The effects of the processing temperature on the mechanical and electrical properties of the wires based on CNTs@AA-6101 and graphite@AA- 6101 composites were investigated by electron microscopes, thermogravimetric analysis, tensile tests, conductor tests and Raman spectroscopy. The results show that CNTs were successfully incorporated on the surface of aluminum wires; the tensile strength of CNTs@AA-6101 increased by 30% and 34% as compared to graphite@AA-6101 and standard AA-6101 wire without CNTs, respectively. Moreover, the resistivity had a decrease 13.7% less than conventional wires. The solubilization process added with the incorporation of CNTs represents a new way for manufacturing nanostructured power cables to achieve high-performance energy transmission lines.

Effect of dispersion method in the production of Al-CNTs nanocomposites
Sónia Simões, Filomena Viana, Marcos A. L. Reis and Manuel F.Vieira
Microscopy and Microanalysis, v. 22 , Issue S4, pp. 52-53, 2016
https://doi.org/10.1017/S1431927616000453
Publicado: 14/03/2016
Abstract
This research is focused on the study of CNTs dispersion in Al-CNTs nanocomposites. The nanocomposites were produced by conventional powder metallurgy route. CNTs used in this work (from composites Fibermax) are mostly multi-walled CNTs (MWCNTs) and powders of aluminum (from Goodfellow) exhibit a maximum particle size of 60 µm. The CNTs dispersion through matrix was made using two approaches: (1) the dispersion of CNTs and mixture with Al powders performed in a single step as describe in previous work [3] and (2) the CNTs were untangle previously by ultrasonication in propanol for 15 min and then mixed with Al powders by ball milling in propanol during 6 h with a ball-to-powder ratio of 20:1. Microstructural characterization of Al-CNTs nanocomposites was performed by optical microscopy (OM), scanning and transmission electron microscopy (SEM and TEM), electron backscattered diffraction (EBSD) and high resolution transmission electron microscopy (HRTEM). To evaluate the CNTs dispersion, an area of 1609182 µm2 was analysed for each sample using an optical microscope and the software Leica Application Suite.
Microstructural Characterization of Aluminum Carbon Nanotube Nanocomposites Produced Using Different Dispersion Method
Sónia Simões, Filomena Viana, Marcos A. L. Reis and Manuel F. Vieira
Microscopy and Microanalysis, v. 22 , Issue 3, pp. 725-732, 2016
https://doi.org/10.1017/S143192761600057X
Publicado online: 08/03/2016

Abstract
This research focuses on characterization of the impact of dispersion methods on aluminum-carbon nanotubes (Al-CNTs) nanocomposite structure. Nanocomposites were produced by a conventional powder metallurgy process after the dispersion of the CNTs on the Al powders, using two approaches: (1) the dispersion of CNTs and mixture with Al powders were performed in a single step by ultrasonication; and (2) the CNTs were previously untangled by ultrasonication and then mixed with Al powders by ball milling. Microstructural characterization of Al-CNT nanocomposites was performed by optical microscopy, scanning and transmission electron microscopy, electron backscatter diffraction, and high-resolution transmission electron microscopy (HRTEM). Microstructural characterization revealed that the use of ball milling for mixing CNTs with Al powders promoted the formation of CNT clusters of reduced size, more uniformly dispersed in the matrix, and a nanocomposite of smaller grain size. However, the results of HRTEM and Raman spectroscopy show that ball milling causes higher damage to the CNT structure. The strengthening effect of the CNT is attested by the increase in hardness and tensile strength of the nanocomposites.

Study of Oxidation States with Heating on Charge Transport of the Graphene Nanoribbon
Mário Edson Santos de Sousa, Marcos Allan L. dos Reis and Jordan Del Nero
Journal of Nanoscience and Nanotechnology, v. 16, n.1 , pp. 213-26, 2016
https://doi.org/10.1166/jnn.2016.10678
Publicado: jan/2016
Abstract
In this paper, we present a study based on extended Hückel (ETH) and the Green function of the electron transport in a graphene nanoribbon with a nanopore oxidized in the middle. We consider several types of oxidation:hydroxyl, carboxyl and ketone groups adsorbed in edges, pore and surface of the riddon. The results indicate that nanoribbons with medium and high oxidation are more thermally stable than the low oxidation nanoribon that shows greater sensitivity at 120 °C. Finally, Ohmic and Negative Differential Resistance (NDR) were obtained from I(V) curves, thus was possible determine the current peaks and threshold voltages (VTh1 <VTh2 <VTh3 <VTh4), which correspond to quantum transport of the nanoribbon not oxidized, high-oxy, med-oxy and low-oxy, respectively, so creating two nanoconstrictions as well as two regions of quantum confinement.
TEM and HRTEM characterization of nanocomposites reinforced with carbon nanotubes
S. Simões, F. Viana, M. A. L. Reis, M. F. Vieira
Microscopy and Microanalysis, v. 21 , S6, pp. 86-87, 2015
https://doi.org/10.1017/S1431927614014135
Publicado online: 10/09/2015

Abstract
This investigation focus on the production of aluminium matrix composites reinforced with CNT, by powder metallurgy techniques. CNT used in this work (from FIBERMAX composites) are mostly multi-walled CNT agglomerated in large clusters. The characterization of CNT was performed by scanning and transmission electron microscopy (SEM and TEM) and high resolution transmission electron microscopy (HRTEM). The dispersion of CNT was carried out using an ultrasonicator during 15 minutes in isopropanol. Figure 1 shows that this dispersion treatment was effective to untangle the CNT clusters. To produce the composites, Al powders (from Goodfellow), with a maximum particle size of 50 m and a purity of 99.5 %, were mixed with CNT in a Turbula during 1h. Mixtures of Al powders and CNT (0 to 2 wt.%) were hot pressed and sintered at 600 ºC during 90 min under a pressure of 50 MPa, with a vacuum of 10-2 Pa.
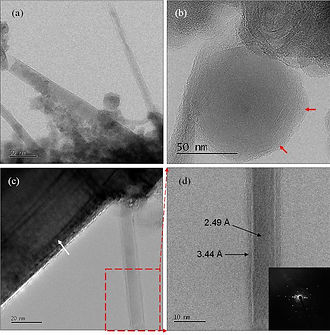
One-Step Synthesis and Characterization of a Nanocomposite Based on Carbon Nanotubes/Aluminum and Its Reinforcement Effect on the Metal Matrix
Marcos Allan Leite dos Reis, Elizabeth M. S. Rodrigues, Jordan Del Nero, Sónia Simões, Filomena Viana, Manuel F. G. Vieira and Maria T. F. Vieira
Journal of Materials Science and Engineering B, v. 5, issue 7-8, pp. 311-319, 2015
DOI: 10.17265/2161-6221/2015.7-8.009
Publicado: 08/2015
Abstract
The nanocomposite based on carbon nanotubes/aluminum (CNT/Al) was one-step prepared by the DC arc discharge method under an argon/acetone mixed atmosphere. Synthesis was performed by arc plasma on a pure graphite rod, filled by aluminum powder as an anode and aluminum plate as a cathode. Discharge conditions of 85 A and 20 V were used at a pressure range of 375 to 750 Torr. The CNT/Al was characterized by Scanning Electron Microscopy with Energy Dispersive Spectroscopy; Transmission Electron Microscopy; Laser Diffraction Particle Size Analysis; X-Ray Diffraction; Raman Spectroscopy; Thermogravimetric Analysis; and, its reinforcement effect of the CNTs on the aluminum matrix was measured by Vickers microhardness test. This nanocomposite shows agglomerates of multiwalled carbon nanotubes filled with Al4C3 and blended with aluminum particles; moreover, in the nanocomposites was found a hardness increase of 40% for nanocomposites with 1.0 wt.% of CNT/Al.
Design and Simulation of Nano-Logic Gates Based on p–n Junction with Carbon Nanotube Electrodes
Mayara P. Rodrigues, Mário Edson S. de Sousa, and Marcos A. L. dos Reis
Journal of Computational and Theoretical Nanoscience, v. 12, n. 8, pp. 1802-1806, 2015
https://doi.org/10.1166/jctn.2015.3961
Publicado: 08/2015

Abstract
This paper reports a design and simulation of a logic cell based on p–n junction linked at sidewall of Carbon Nanotube (CNT) electrodes. The novel concept shows both sidewall functionalized armchair CNTs linked themselves through biphenyl with electron donor and electron acceptor groups. Electrical simulation results show Negative Differential Resistances (NDRs) by tunnel effect that originates the 0-bit and 1-bit with an on/off current ratio of 3.0 under low voltage, as well as the influence of temperature on the current peak was analyzed when the device was heated from 27 °C to 100 °C. This logic cell array will provide a new insight for building nanotube interconnections and unit for logic gates.

Influence of dispersion/mixture time on mechanical properties of Al–CNTs nanocomposites
Sónia Simões, Filomena Viana, Marcos A.L. Reis, Manuel F. Vieira
Composite Structures, v. 126, pp. 114-122, 2015
http://dx.doi.org/10.1016/j.compstruct.2015.02.062
Publicado online: 12/02/2015
Abstract
The influence of dispersion/mixture time on microstructural evolution and mechanical properties of aluminum matrix nanocomposites reinforced by carbon nanotubes (Al–CNTs) were investigated in this study. The nanocomposites were produced by conventional powder metallurgy routes. The microstructure was characterized by scanning electron microscopy (SEM), electron backscattered diffraction (EBSD) and high-resolution transmission electron microscopy (HRTEM). Microstructural analysis shows clusters of carbon nanotubes (CNTs) mainly at the grain junctions, but also CNTs well dispersed and embedded in the aluminum matrix. A strong strengthening effect of the CNTs on the aluminum matrix was measured for the nanocomposites produced with 15 min of dispersion/mixture time. For shorter times than 15 min, it is not possible to obtain a dispersion, which can lead to a reinforcement of the aluminum matrix, while longer dispersion/mixture times cause a decrease in mechanical strength due to the damage caused by the increase in the number of defects and junctions of CNTs.
Improved dispersion of carbon nanotubes in aluminum nanocomposites
Sónia Simões, Filomena Viana, Marcos A.L. Reis, Manuel F. Vieira
Composite Structures, v. 108, pp. 992-1000, 2014
http://dx.doi.org/10.1016/j.compstruct.2013.10.043
Publicado online: 31/10/2013

Abstract
In this study, we investigated the influence of the dispersion technique of carbon nanotubes (CNT) in the production of aluminum matrix nanocomposites. Three production routes using different dispersion techniques were tested: in R1 route the CNT were dispersed using an ultrasonic bath; in R2 route the dispersion was achieved by ultrasonication, while in R3 route the dispersion and mixing were performed by ultrasonication CNT and Al powders. Nanocomposites with several CNT contents (0.25–2.0 wt.%) were produced by conventional powder metallurgy procedures. Microstructural characterization by scanning and transmission electron microscopies revealed that the best dispersion of the CNT is obtained using R3 route. Nanocomposites with 0.75 wt.% of CNT exhibit well dispersed and embedded nanotubes and the highest hardness and tensile strength. The observed 200% increase in the tensile strength attested the strengthening effect of the CNT and the efficiency of the new dispersion treatment (R3 route).

The Charge Transport in (2, 2) Armchair Carbon
Nanotube: A Theoretical Modeling
Alex Venício de Abreu Moreira, Mário Edson Santos de Sousa, Alex Amaral Cabral, Julia Helena da Silva Martins, and Marcos Allan Leite dos Reis
Journal of Computational and Theoretical Nanoscience, v. 10, n. 10, pp. 2398-2402, 2013
https://doi.org/10.1166/jctn.2013.3221
Publicado: 10/2013
Abstract
Carbon nanotubes are excellent charge transports due to the relationship between the length–diameter in the order of microns to nanometers, respectively, thus being characterized as ballistic conductors and excellent materials for field emission applications in electronic devices. We study the Fowler-Nordheim formalism and first-principles calculations of metallic (2, 2) singlewall carbon nanotube with a diameter of 0.24 nm. Our results are consistent for field emission devices nanostructured with these specifications. Summarize the following results: (i) for the both methods used the same trend I–V; (ii) exponential behavior and quasi-ballistic, indicating the proportionality between I and V characteristic of (2, 2) carbon nanotube armchair, (iii) tendency of inelastic tunneling under intense field electric, which is consistent with studies on inelastic electron tunneling spectroscopy (IETS); (iv) matching number Mulliken charge for using the formalism of the Fowler-Nordheim equation to reduce the computational first-principles calculations for this (2, 2) carbon nanotube.
Study of Ink Paper Sensor Based on
Aluminum/Carbon Nanotubes
Agglomerated Nanocomposites
Marcos A. L. dos Reis, Augusto F. Saraiva, Manuel F. G. Vieira, and Jordan Del Nero
Journal of Nanoscience and Nanotechnology, v. 12, n. 12, pp. 1–6, 2012
https://doi.org/10.1166/jnn.2012.6145
Publicado: 09/2012

Abstract
Agglomerated nanocomposites based on Aluminum/Carbon Nanotubes (Al/CNT) were produced by an arc discharge technique under argon/acetone atmosphere and ultrasonically dispersed in distilled water to form an ink-like composite. This ink was spread onto commercial paper to produce a conductive thick film. Experimental results show that the electrical resistance of Al/CNT nanocomposite on paper changes when a mechanical stress and/or heat is applied. The multisensory properties obtained are the following: i piezoresistive effect, electrical resistance shows linear dependence with pressure intensity at room temperature; ii polynomial relationship between electrical resistance and temperature; and iii high accuracy thermal sensor compared to a K type thermocouple at 25 C. The nanocomposite and paper morphology was analyzed by Scanning Electron Microscopy with Energy Dispersive Spectrometry (SEM/EDS) and a favorable surface for physisorption was observed. Transmission Electron Microscopy (TEM) was utilized for Al/CNT agglomerated indicating that the ink paper based on nanocomposite shows good performance as a thermo-piezoresistive sensor.